Revolutionising upstream design processes with digital twins
Ensuring the design team and stakeholders work together is crucial at the start on any large capital project. Collaboration is essential when it comes to working with many different groups, partners, subcontractors, and inter-departmental personnel, as they work with multiple information sources and make numerous design changes as part of the review process. Failure in any of these work processes can result in costly mistakes once handover is complete as the project moves into construction - and even more so as it moves into operations. Lengthy project delays and subsequent operational downtime is expensive.
This scenario, which had been typical among engineering firms, is one that NOV Inc. wished to avoid.
NOV Inc., a global company headquartered in Houston, Texas, delivers technology-driven solutions to the global energy industry, including solutions supporting digital and smart oilfield initiatives. The NOV Wellstream Processing division supplies equipment and solutions for all the activities NOV performs when separating and treating oil and gas as part of an upstream production facility.
This article examines how NOV overcame the problem of remote collaboration by having a unified view of their federated data from multiple sources provided by PlantSight, the digital twin cloud-based service developed by Bentley Systems and Siemens to support distributed/remote collaborative processes and engineering 3D design and operations.
Solving the Problem of Remote Collaboration
Previously, NOV used Navisworks to share designs with fabricators or subcontractors, since it was a widely used review application in the oil and gas sector and could accept multiple file formats. One of the main disadvantages of the platform was the inability to track changes and versions across the disciplines. Therefore, identifying which model was the main ‘source of truth’ proved difficult when there was more than one file being used. In addition, NavisWorks uses snapshots of the design files, and keeping this information up to date is impossible. Furthermore, sharing files can lead to security lapses since other parties could potentially extract information from them. The inability to bring the many discipline-specific models and files together for review to enable the design team to share information with all stakeholders around a single plant model and resolve issues quickly was a major challenge for NOV.
NOV overcame these problems by switching to PlantSight, as the models for the project can be securely shared in the cloud with partners and are always kept up to date. PlantSight pulls the latest information in real time from the design tools, and changes are instantly fed back to the originating system, showing a complete audit trail of when a change was made, why, and by whom. Models are protected, and it is possible to control which parts of the project a partner or client can see.
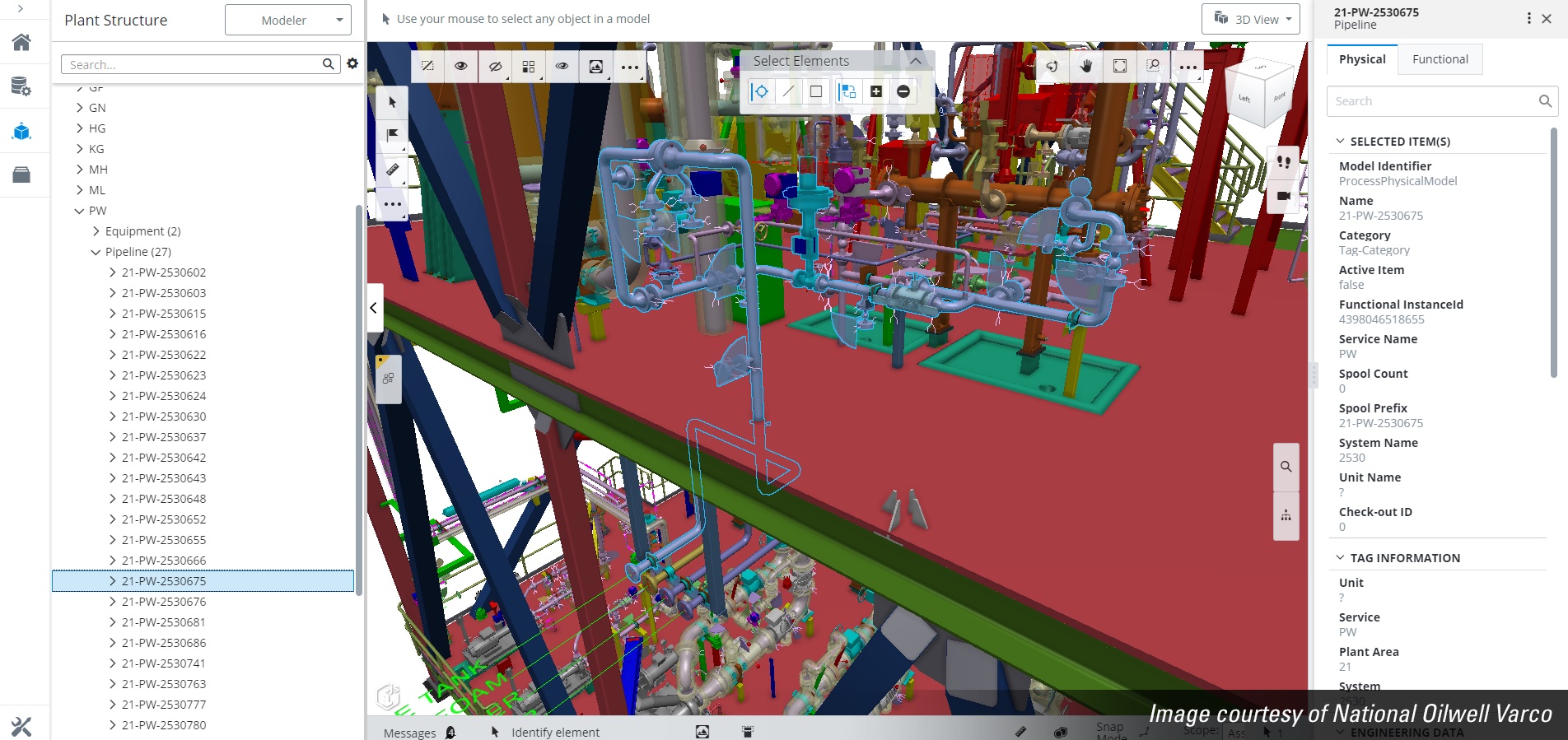
NOV System.
Solution Selection and Digitalisation
NOV had scanned the market and did not find any other tools with the same level of openness and flexibility as PlantSight. The capability to integrate the digital twin solution with many other tools increased NOV’s confidence in the software. Already a user of Bentley’s OpenPlant design application, NOV could seamlessly integrate their design review work processes between OpenPlant and PlantSight to take advantage of real-time change management, issue resolution, and clash detection features. As NOV was already familiar with Bentley applications, PlantSight came at a relatively low cost and did not incur any additional training costs, and the transition would cause minimal disruption.
One additional hurdle was convincing management to switch to PlantSight, as they were not involved with projects on a day-to-day basis. However, they realized and understood that it would be inefficient to create a digital twin using the old method of pulling together a review model on a single system with everyone, then commenting on the overall design during a review meeting. Management were convinced of the digital twin solution due to the transformation they saw with the potential for savings and the significant benefits of remote collaboration and reviews in real time. This proved advantageous when the COVID-19 pandemic struck just after the start of the project, as PlantSight could help all project team members collaborate from home while working simultaneously on shared design information.
The overall transition to PlantSight from Navisworks was very smooth. After receiving a two-hour training course and participating in hands-on exercises, they began working on their projects faster with PlantSight.
Keeping the Project on Track
NOV was an early adopter of PlantSight, as they used it before it was officially released in 2019. Working alongside Bentley, NOV’s CAD manager and some key personnel worked on testing iterated versions of the solution to achieve acceptable new digital work processes. The project was able to remain close to the original schedule plan of about six months for preparation and acceptance of the new ways of working for their teams.
While thinking big about digital transformation and digital twins, NOV decided it was best to first prove small. In controlled phases, NOV started their PlantSight implementation with a small group from the 3D layout department and associated personnel making the transition easier to control. Process design and schematics was the next phase, which created further ease of use for piping designers as more information from the upstream design process was made available to them. Previously, the piping designers had to enter a lot of information manually to start their work. Now they could easily reference the existing layout information faster and in real time.
Cloud-based Accessibility and Security
When NOV went live with PlantSight, they moved from server-based to cloud-based software. The transition removed the limitations of specific design files on local servers used by different disciplines working independently, while also eliminating any inconsistencies and rework. With PlantSight, personnel can now work simultaneously on a single, large design, and are immediately notified when clashes are detected and other issues are highlighted. Since PlantSight is cloud based, personnel can access files remotely, where space, security and scalability is never a problem.
With the PlantSight digital twin service, NOV keeps information in one place, controls it in a single environment, keeps it consistently up to date, and makes all data sources accessible. For example, 3D design information, the attributes of piping specifications, and installation notes for the piping are all visible and manageable from a web browser. Previously, if a piping manager wanted a piping layout report, they had to involve a piping designer. Now, the piping manager can use self-service dashboards and reports directly. As well as being able to work faster, collaborate more effectively, and make design changes wherever they are, NOV personnel improved productivity by reducing interruptions and shortening project waiting times. With two dedicated resource personnel, NOV supports 100 engineers on projects that typically have 20 contributors who don’t require much assistance or support.
The Future Outlook
Cloud-based digital twins can quickly demonstrate the benefits of combining engineering, design, build, construction, operations, and maintenance data, including 3D representations and quality-related data. NOV have already gained the benefits of remote and collaborative design reviews and qualification, overcoming common pitfalls such as unreliable information, manual processes, and an unclear line of sight across the design team. They have been able to improve their designs and resolve any issues and potential clashes early in the design phase, so they don’t become expensive problems in the construction or operational phase.
Moving forward, the digital twins in PlantSight are inspiring new ideas for products and processes within NOV. They can modify designs to include remote equipment, and operations can be monitored by feeding live data directly to the models for a complete picture of performance.
Editor's note: This article was taken from an original whitepaper by the ARC Advisory Group, in collaboration with Bentley Systems, entitled:
EARLY USER TESTIMONIALS OF THE CLOUD-BASED, PLANTSIGHT COLLABORATIVE ENGINEERING SERVICE
KEEPING THE ENERGY INDUSTRY CONNECTED
Subscribe to our newsletter and get the best of Energy Connects directly to your inbox each week.
By subscribing, you agree to the processing of your personal data by dmg events as described in the Privacy Policy.