Biden’s Solar Factory Boom Slows as Cheap Imports Flood Market
(Bloomberg) -- President Joe Biden’s signature climate law unleashed a $16 billion flood of promised investments in solar manufacturing, as companies unveiled plans for factories across the US and raised hopes of eroding China’s green tech dominance.
But less than two years later, manufacturers have quietly shelved or slowed plans for at least four of those plants. High borrowing costs and record-low panel prices — the result of cheap imports pouring into the market — have made some projects uneconomical. The decisions underscore the limits of US government subsidies when it comes to wresting control of established clean energy supply chains from China.
“The incentives in the Inflation Reduction Act really put us in a position in the United States to have a lot of announcements and a lot of hope,” said Mike Carr, executive director of the Solar Energy Manufacturers for America Coalition. But market conditions have created “some pretty stiff headwinds when it comes to new manufacturing investments.”
The US already tried — and failed — more than a decade ago to nurture a domestic solar supply chain. But a series of intermittent tax incentives and tariffs were no match for the brute force of China’s commitment to dominate the market. Most of the factories built as part of that manufacturing push have long since shuttered.
Now, plant delays and cancellations are intensifying pressure on Biden to prevent a repeat. Following the IRA’s enactment, companies proposed building or expanding US manufacturing capacity for a range of equipment used in solar projects, representing $16 billion in investments, according to the American Clean Power Association. Some of those plans are at risk.
As soon as this week, the administration is expected to expand existing tariffs so they include the two-sided panels that make up the vast majority of US imports, according to people familiar with the matter. And Biden will announce on Tuesday an increase in some so-called Section 301 tariffs, including on solar cells, though the administration has signaled to industry stakeholders it will also begin moving to exclude some critical machinery used to make panel components.
Manufacturers also want the White House to vigorously enforce a deadline for using other panels that were imported tariff-free under a Biden administration moratorium set to expire July 6. And some panel makers have asked the federal government to impose new duties on cells and panels coming from southeast Asia, arguing they are being sold below production costs.
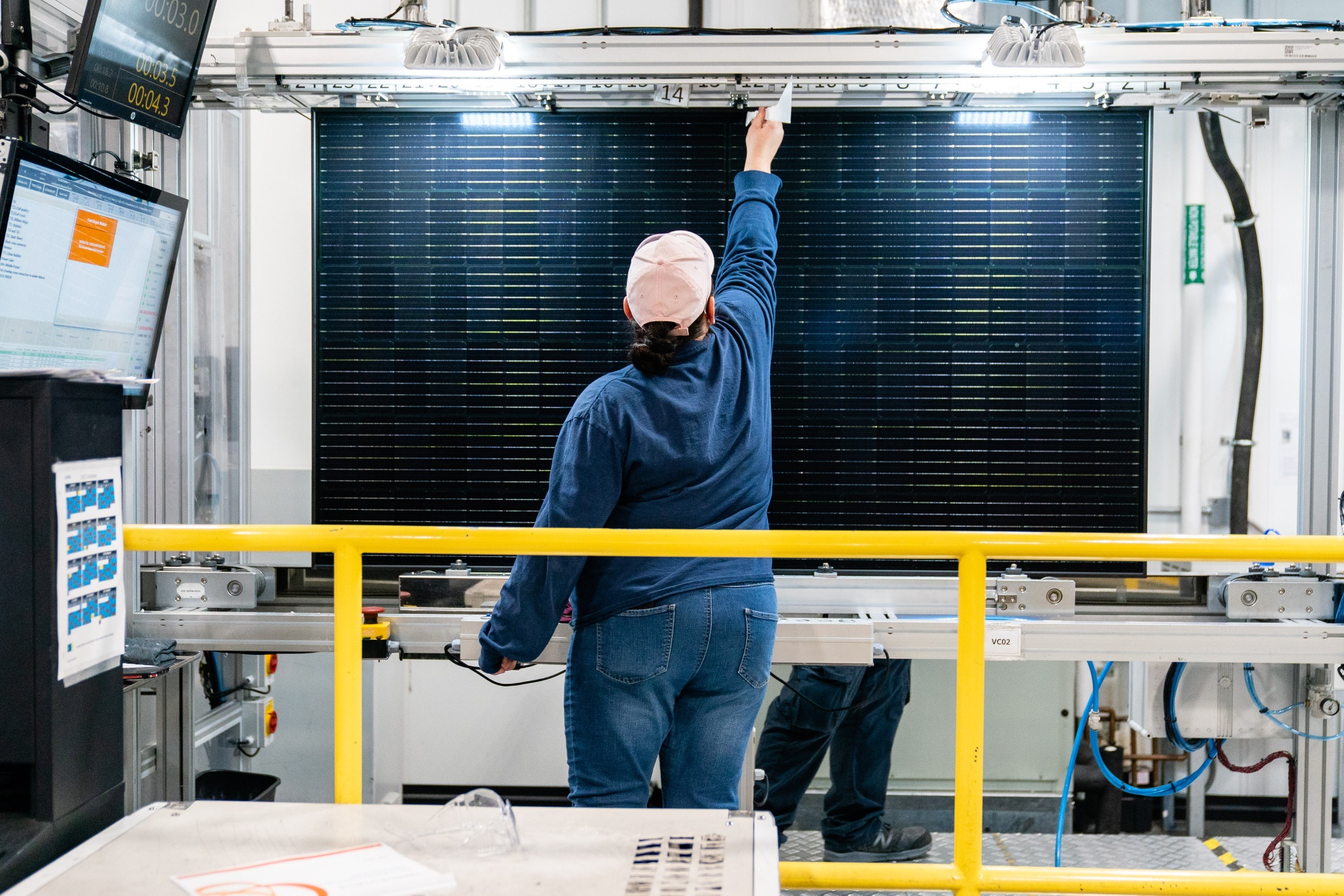
Manufacturers have slowed timelines for some of the proposed US plants and pulled the plug on at least one of them. Some are waiting for government guidance on how much they’ll benefit from a tax credit meant to incentivize domestic content in renewable projects.
Enel SpA, for example, sought to build a factory for solar cells and modules in Oklahoma, through its affiliate 3Sun USA LLC. The project was first announced in 2022, with plans to begin construction in fall 2023 and start initial production this year. But construction still hasn’t begun and now Enel’s new leadership is shifting spending toward higher-margin projects and regions.
“3Sun USA is currently engaged in finding a majority financial partner for the project," an Enel spokesperson said. "This is a condition for the project to proceed to construction. The company will provide further updates in due course.”
In San Antonio, Texas, Mission Solar Energy had aimed to more than triple its manufacturing capacity to 1 gigawatt annually in 2024. Although the company expanded the size of its production facility — holding a ribbon cutting this month — it hasn’t begun ordering and installing equipment to boost output, company spokeswoman Laura Waldrum said. Completion of that phase “will depend on market conditions, such as demand and competition from imports,” she said. “Currently, we do not have a definitive timeline for project completion.”
The Massachusetts technology firm CubicPV Inc. in February pulled the plug on its plans for a US solar wafer factory, citing “a dramatic collapse” in prices.
Even where projects are proceeding, timelines have slipped.
For instance, Canada-based Heliene Inc. is still working to build another gigawatt of panel production capacity in Minnesota, which would more than double its current output. But instead of bringing all of that online this year, as originally announced, Heliene now intends to install half of it in 2025. Martin Pochtaruk, the company’s president, said the shift was prompted by “overall market instability and out-of-control import levels.”
While Biden’s Inflation Reduction Act was seen as the first-ever US industrial policy for solar, it’s turned out to be a lopsided one, focusing some subsidies on panel-making at the final assembly stage of the supply chain instead of the start of it, where key components such as ingots and wafers are made. Companies can win advanced manufacturing tax credits to help pay for those upstream fabrication facilities, but under current Treasury Department guidance they don’t benefit from a separate subsidy meant to encourage domestic content in renewable power projects.
Solar manufacturers are lobbying the Biden administration to revise its initial guidance for claiming that domestic content tax incentive so it better encourages renewable power developers to use panels made with US-produced wafers and other subcomponents. Changes could come as soon as this week, according to people familiar with the matter.
There are bright spots. First Solar Inc. has expanded US production capacity for its thin-film panels. Qcells North America has already boosted capacity at a panel-making plant in Georgia and is building another factory to produce solar ingots, wafers, cells and finished panels. And in Ohio, Invenergy LLC and LONGi Green Energy Technology Co. began producing panels at their Illuminate USA plant earlier this year.
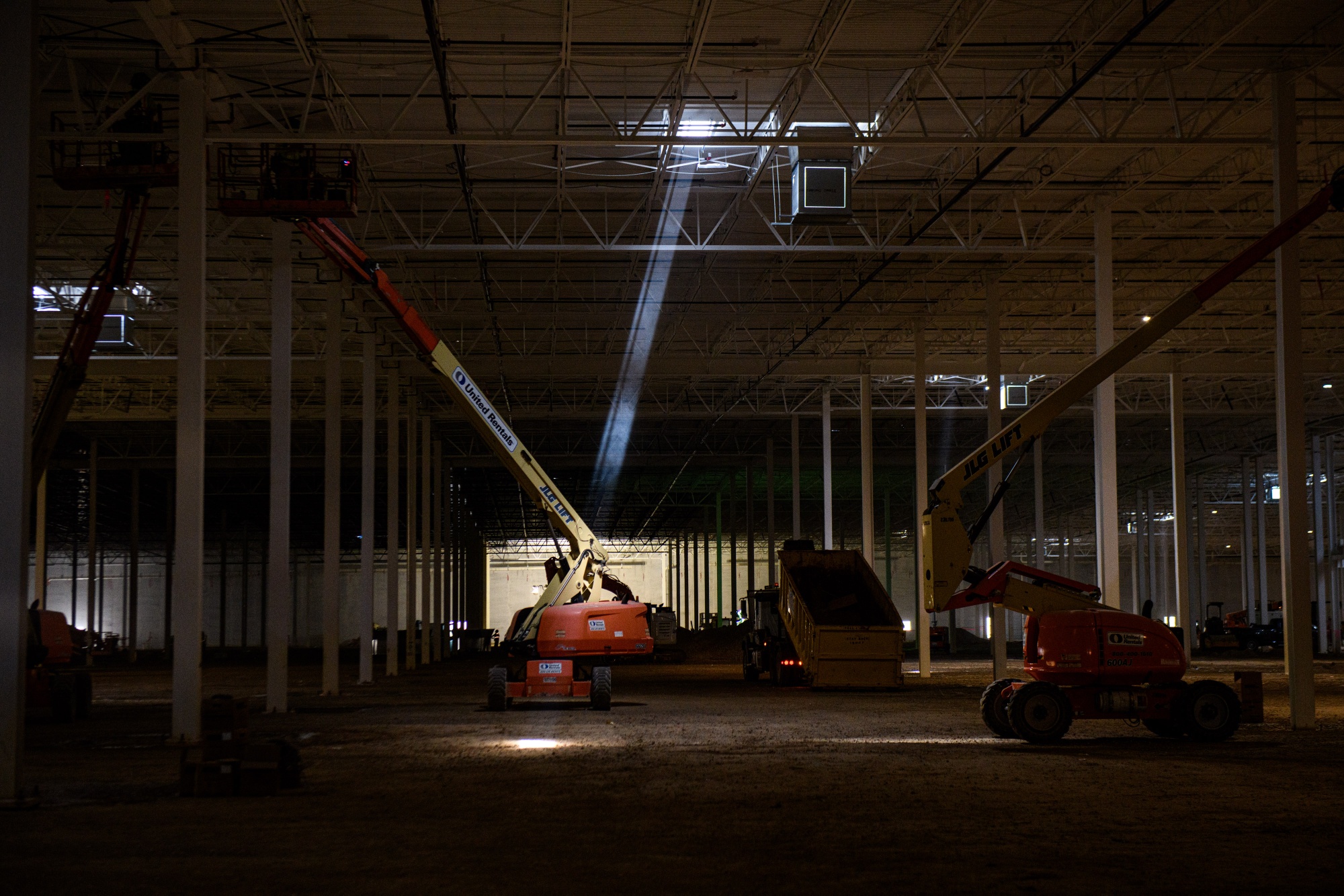
While the growth in US panel-making is likely to boost demand for locally made components, “it’s pretty hard to build a factory and to make it competitive with everything that’s going on,” said Art Fletcher, Invenergy’s head of domestic content, at the BloombergNEF summit in New York last month. “We have a burgeoning industry that is just starting to stand up, and we’ve got to protect that industry.”
(Adds Biden announcement plans in sixth paragraph.)
©2024 Bloomberg L.P.
KEEPING THE ENERGY INDUSTRY CONNECTED
Subscribe to our newsletter and get the best of Energy Connects directly to your inbox each week.
By subscribing, you agree to the processing of your personal data by dmg events as described in the Privacy Policy.
More renewables news
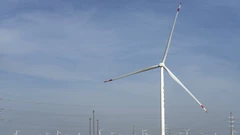
GB Energy Faces Doubts as UK Declines to Affirm Future Funds
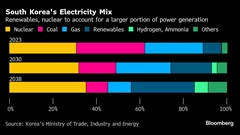
Korea Cancels Planned Reactor After Impeaching Pro-Nuke Leader
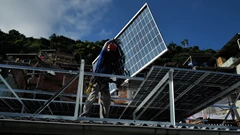
Brazil’s Net-Zero Transition Will Cost $6 Trillion by 2050, BNEF Says
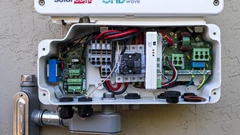
SolarEdge Climbs 40% as Revenue Beat Prompts Short Covering
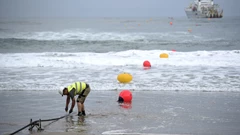
EU to Set Aside Funds to Protect Undersea Cables from Sabotage
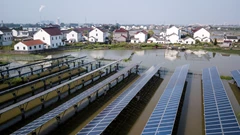
China Revamps Power Market Rules In Challenge to Renewables Boom
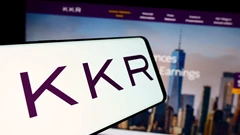
KKR increases stake in Enilive with additional €587.5 million investment
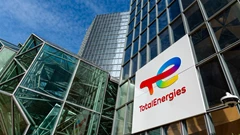
TotalEnergies and Air Liquide partner to develop green hydrogen projects in the Netherlands
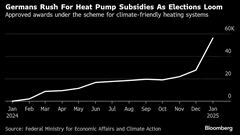
Germany Set to Scale Down Climate Ambitions
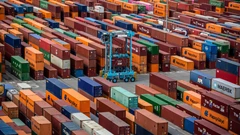