Linde and Evonik work on joint hydrogen solution
Linde and Evonik Industries offer a fully integrated, holistic solution that brings together various technologies to separate hydrogen.
Currently there is growing interest in the prospect of using the existing natural gas infrastructure more extensively to transport hydrogen (H2) – green H2 in particular. Numerous initiatives have already been launched around the world in order to develop enabling technology concepts. Existing pipeline networks could be used to efficiently transport H2 over long distances and deliver it to end points along this infrastructure, where it could be fed into industrial applications or provide a source of energy.
For this to happen, however, the hydrogen must be efficiently separated from the natural gas blend at the point of extraction. Linde and Evonik’s solution combines pressure swing adsorption (PSA), a technology in which Linde has decades of experience, with high-performance “HISELECT powered by Evonik” membranes to deliver hydrogen at purity rates of up to 99.9999 percent.
“This high-purity stream of hydrogen could then be delivered to fuelling stations, for example, to power fuel-cell vehicles. But it’s not just a source of energy; it’s also a valuable feedstock especially for the chemicals industry,” explains Jürgen Nowicki, Executive Vice President of Linde plc and CEO of Linde Engineering.
“We already have technologies on the market; technologies that are ready to use as soon as the market signals increased uptake for H2 blending into natural gas networks and the corresponding need for separation processes,” adds Nowicki.
This offering also strengthens Linde’s position as a leading provider of hydrogen technologies and applications.
A demo plant at the Linde Dormagen site in Germany will act as a showcase for the efficiency and cost effectiveness of this technology. “The economic viability of extracting hydrogen from the current natural gas infrastructure depends largely on the efficiency of the gas separation technology. Membrane selectivity is a key success factor,” explains Dr. Harald Schwager, Deputy Chairman of the Executive Board of Evonik. “We are the world’s only fully backward-integrated producer of gas separation membranes. Drawing on our many years of experience in polymer chemistry, we are able to adjust key membrane properties at material level, providing customers with a highly selective and robust separation technology.”
One of the first successful reference cases building on the collaboration between Linde and Evonik in the field of membrane-based gas separation was a helium processing plant in Mankota, Canada, which went on stream in 2016. The two separation processes – membrane and PSA technologies – were also combined in this facility. It was the first helium processing plant of its kind worldwide and now processes more than 250,000 standard cubic meters of raw gas per day to gain industrial-grade helium purity levels (99.999 percent). Following on from this success, Linde and Evonik expanded their collaboration, developing gas separation solutions for natural gas processing, synthesis gas applications and ammonia plants.
“We continue to strengthen our position as a leading provider of all-inclusive separation packages by rounding out our offering with forward-looking solutions for separating H2 from natural gas streams,” concludes Nowicki.
KEEPING THE ENERGY INDUSTRY CONNECTED
Subscribe to our newsletter and get the best of Energy Connects directly to your inbox each week.
By subscribing, you agree to the processing of your personal data by dmg events as described in the Privacy Policy.
More technology news
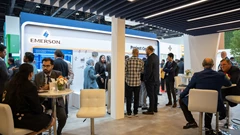
Emerson showcases advanced automation technologies at EGYPES 2025
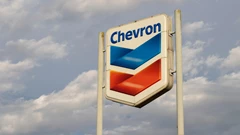
Engine No. 1, Chevron and GE Vernova to power US data centres
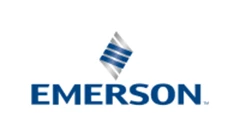
Emerson to complete buyout of AspenTech for $7.2 billion
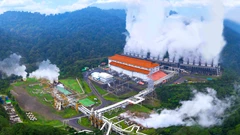
SLB and Star Energy Geothermal announce technology collaboration
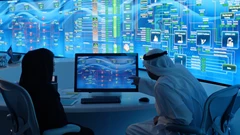
ADNOC and AIQ successfully complete trial phase of agentic AI solution
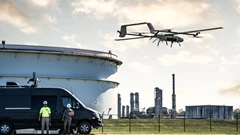
Phoenix Air Unmanned achieves single-day pipeline patrol milestone
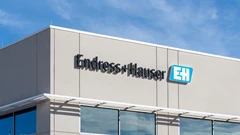
Endress+Hauser integrates SICK’s gas analysis and flow measurement technology
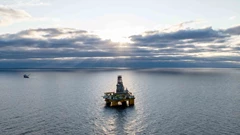
SLB awarded multi-region deepwater contracts by Shell
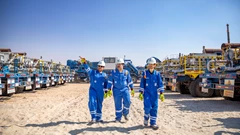
ADNOC Drilling, SLB and Patterson-UTI close Turnwell joint venture
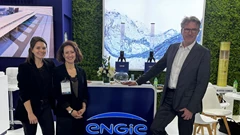