Shell’s QGC business is at the forefront of using digital technologies
Shell’s QGC business is located in Queensland in Eastern Australia. They are one of Australia’s leading natural gas producers, focused on developing Queensland’s world-class onshore gas reserves. Shell’s QGC business produces natural gas to supply the Australian domestic market and for export as LNG via our two-train LNG liquefaction plant on Curtis Island in Queensland. QGC produces natural gas from the Surat Basin of southern Queensland and supplies domestic and international markets.
Every day there are around 1,400 people safely going about their work in our business – maintaining over 7,000 kilometers of gathering pipelines and 25 processing facilities, inspecting more than 3,160 wells. Therefore, it is imperative that team members arrive on the site equipped with the right parts and the right information to carry out their work.
Challenge
To send personnel into the field with the right information so their time is not wasted, critical and relevant engineering information, typically held across many different systems, needs to be quickly and easily accessible. The information also needs to be up to date and accurate, with any changes managed and tracked.
Breakthrough
To make their information readily accessible, Shell’s QGC business implemented Bentley’s AssetWise ALIM as an engineering data warehouse establishing a master tag registry to maintain data integrity and initially storing more than 20 million data points. Later, in order to provide online access while out in the field and support the growing information needs of the business, they moved their ALIM implementation to the Azure cloud, providing a single portal of engineering data with consistent informational integrity. Now, Shell’s QGC business is doubling the number of documents and model files (and the associated data points) in AssetWise migrating project documentation from an EPC-based system to their digital twin environment.
Outcome
Shell’s QGC business maintenance crews drive over 1 million kilometers per month and arrive on site with the right information to do the work saving time and money. Their operations have also improved efficiency with less data search time and fewer application licenses, and they have increased the accuracy of their information.
Collaboration with their many engineering contractors has been strengthened with enhanced transparency between the design and engineering functions. Information updates are scheduled and delivered to Shell by contractors with minimal manual intervention. The system has enabled the re-use of original engineering design on Brownfield projects reducing design time and costs.
KEEPING THE ENERGY INDUSTRY CONNECTED
Subscribe to our newsletter and get the best of Energy Connects directly to your inbox each week.
By subscribing, you agree to the processing of your personal data by dmg events as described in the Privacy Policy.
More technology news
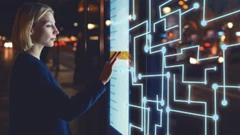
Abu Dhabi’s ADQ and Energy Capital in $25billion deal to power data centres
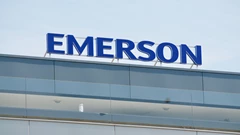
Emerson finalises acquisition of AspenTech for $7.2 bn
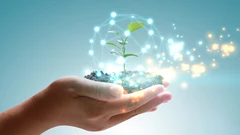
Baker Hughes and Woodside Energy to develop small-scale decarbonisation solution
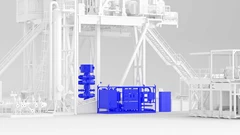
SLB electrifies well control with new technology to boost drilling safety
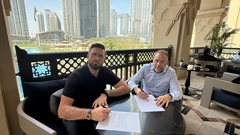
SmartSea and Digital Energy AI to offer innovative solutions for the maritime industry
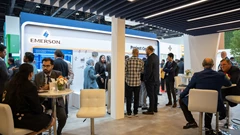
Emerson showcases advanced automation technologies at EGYPES 2025
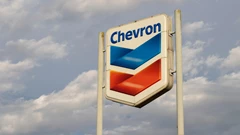
Engine No. 1, Chevron and GE Vernova to power US data centres
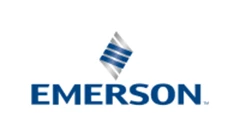
Emerson to complete buyout of AspenTech for $7.2 billion
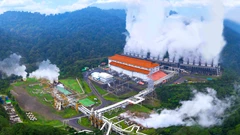
SLB and Star Energy Geothermal announce technology collaboration
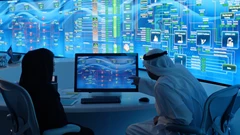