Well optimisation and enhanced recovery through tailored chemistry solutions in Nigeria
Nigeria is one of the largest oil producers in Africa and a key player in the oil and gas industry. With new explorations set to boost production, the country shows no signs of slowing down. To meet the growing demand for energy, operators in the country are looking for ways to maximise production from existing developments while ensuring their operations are as efficient and cost effective as possible.
As wells mature and more hydrocarbon is extracted from the reservoir, the water table in the reservoir rises, causing more water production and increasing the potential for scale deposition. This produced water often contains residual quantities of oil and, in many cases, solid particles. It is imperative to limit or prevent emulsifications from forming, which can impact output efficiency, and proactively control the formation of sulphate and carbonate scales to maintain flow assurance and the integrity of the production system.
Any oil left in the water can potentially waste the time and money spent bringing it to the surface, so separating even small amounts of oil from water can lead to increased revenue. Reusing water can be an alternative option. However, when produced water is used to supply a water-flood or steam-flood program, it must be clean. Oil and solids can quickly foul expensive water-softening resin beads. Dirty water can also require costly maintenance programs for injection wells. Many types of equipment are used to separate as much oil from water as possible, and a bespoke chemistry program is considered the most viable method to improve equipment efficiencies and reduce overall project costs.
ChampionX, a global leader in chemistry solutions and highly engineered equipment and technologies that help companies drill for and produce oil and gas safely and efficiently around the world, was contracted by a major independent operator in Nigeria to develop and test a customised water clarifier solution to treat the produced water outlet of their first-stage separator.
Produced water treatments
Before operators in Nigeria can decide the best plan of action to support production optimisation, they must ensure they meet strict and varying government requirements for water discharge. Several conventional methods are available to treat produced water. However, in this project, the use of hydrocyclone technology was preferred by the operator (Figure 1).
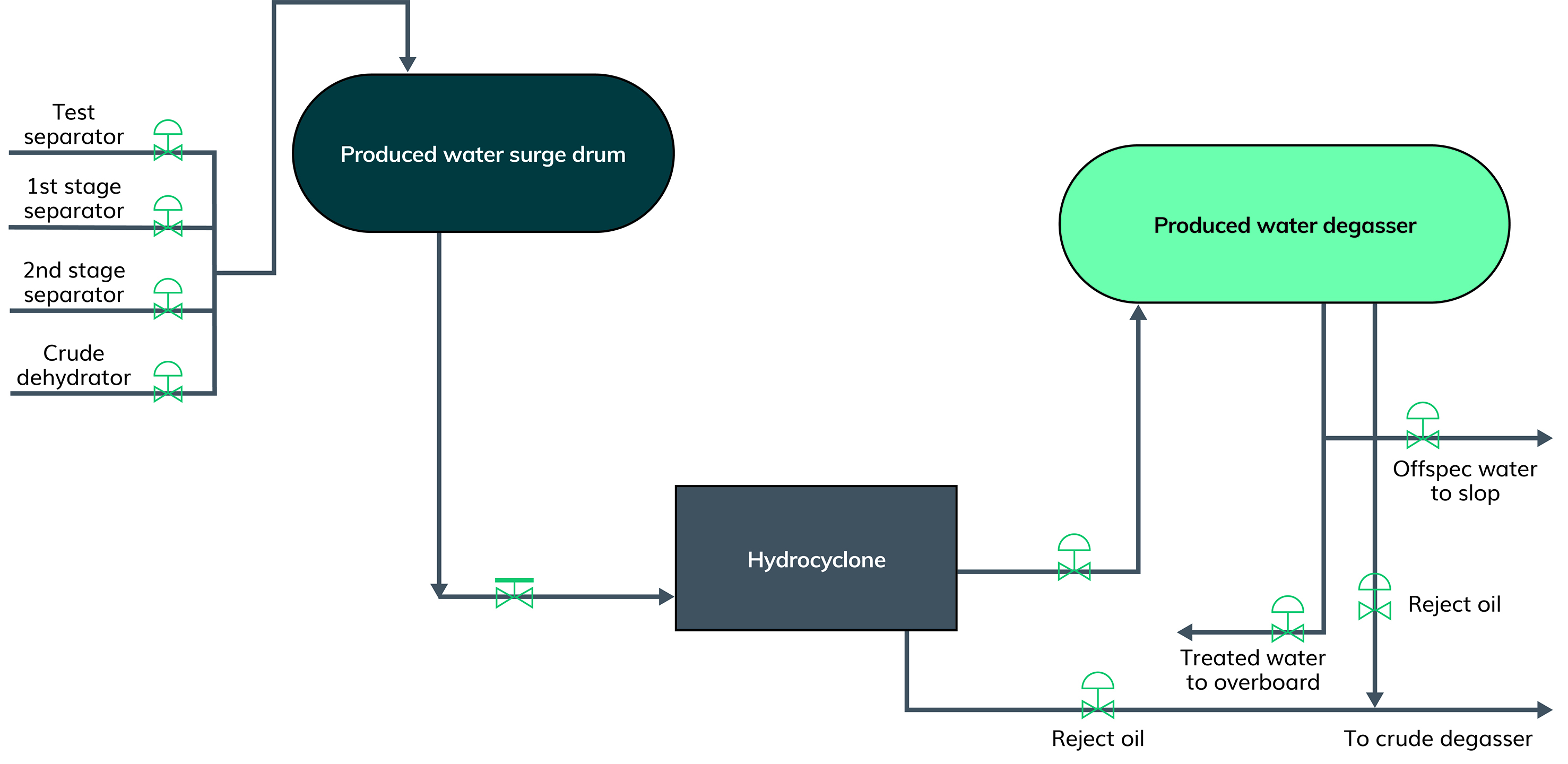
Figure 1: Produced water process flow
Here, produced water from the separators is introduced indirectly through a rectangular port in a conically shaped chamber. As the water rotates rapidly around the chamber, and moves downward, the decreasing diameter causes high centrifugal acceleration of the water to the outside wall, pushing lighter oil droplets to the center of the cone. The oil rises to the top and flows out and the water then exits the bottom of the cone.
Improving water clarifier efficiency
The operator had been experiencing issues with extremely high oil-in-water (OIW) content in the produced water from their first-stage separator. This averaged approximately 3,500ppm going to the produced water surge drum (PWSD). The hydrocyclone was out of service, so the off-spec produced water was being sent to the slop tank to stabilise for a minimum of 48-hours before it could be disposed. This process often still led to a failure to meet government discharge regulation limits, so the water had to remain in the slop tank until it met the required specifications. An incumbent’s water clarifier had been applied to the produced water, but it did not decrease the OIW content.
To address the problems associated with persistent effluent quality, ChampionX was contracted to perform a series of on-site static bottle tests to evaluate their water clarifier product efficiency and put forward the most effective chemistry treatment. The bottle testing used clear, calibrated six-ounce prescription bottles, which conveniently held 100ml of produced water. The tested treatment dosages ranged from 50ppm to 500ppm.
After the water clarifiers were applied, the samples were agitated, observed visually to assess the clarity of the water for benchmarking purposes, and graded between one and ten. This process showed that water clarifier CLAR16029A performed the best of all the chemistries tested to achieve the specification required.
An optimised solution
Over one month, the water clarifier was injected at the produced water outlet of the first-stage separator at a startup dosage rate of 7ppm. By the end of the field trial, this rate was optimized to 15ppm.
As both the hydrocyclone and the produced water degasser were bypassed, the produced water was stabilized in the slop tank, and in less than 24 hours, the OIW met the regulatory requirement of less than 40ppm. This compares to more than 48 hours with the previous chemical application. The results of the application on the customer facility are shown in Figure 2.
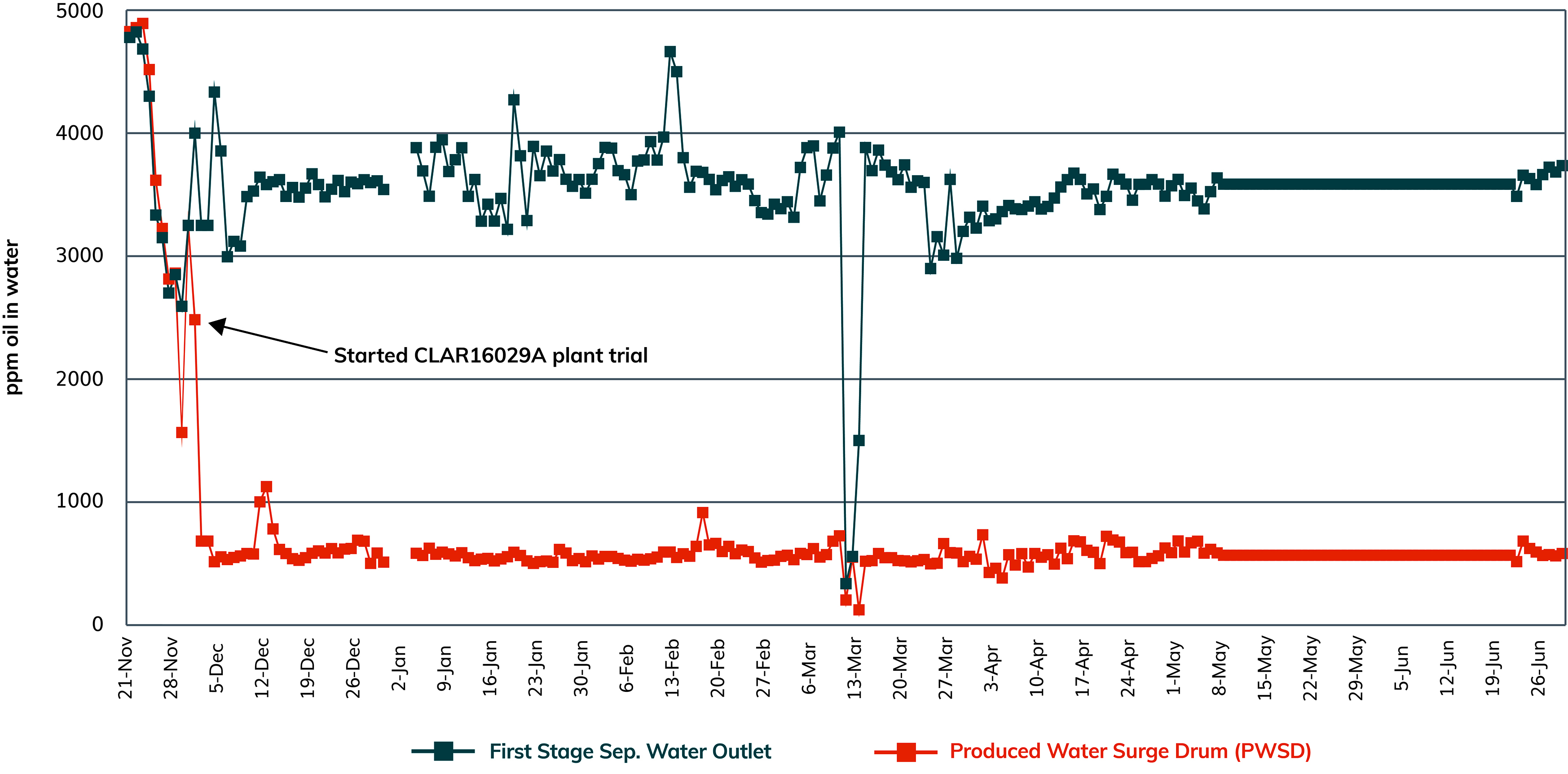
Figure 2: CLAR16029A water clarifier performance results
Enhanced recovery to support sustainability objectives
During the field trial, results demonstrated an increase of 83 percent in oil recovery from the produced water, compared to that recovered before CLAR16029A application, improving recovery whilst reducing operational costs. Following the field trial, the water clarifier was immediately commissioned and the produced water to slop tank practise ended.
The project demonstrated how targeted chemistry solutions can deliver maximised production while improving efficiency. As sustainability objectives remain high on operator agendas, innovative technology is essential to supporting production and environmental goals.
Energy Connects includes information by a variety of sources, such as contributing experts, external journalists and comments from attendees of our events, which may contain personal opinion of others. All opinions expressed are solely the views of the author(s) and do not necessarily reflect the opinions of Energy Connects, dmg events, its parent company DMGT or any affiliates of the same.
KEEPING THE ENERGY INDUSTRY CONNECTED
Subscribe to our newsletter and get the best of Energy Connects directly to your inbox each week.
By subscribing, you agree to the processing of your personal data by dmg events as described in the Privacy Policy.